What about a TV you could roll up?
At the Consumer Electronics Show at the beginning of this year, LG exhibited an OLED TV that automatically ‘rolls away’ into a small drawer. Just like you used to roll out your projection screen to watch your vacation slides in the old days, we’ll soon have a ‘roller TV’ that takes up little space in the corner of the room. And if that sounds a bit like science fiction, you have to remember that we are already using OLED screens – as the display screen in digital cameras, for example, as well as in many smartphones. At the moment, also some high-end TVs use OLED technology.
The major advantages of (AM)OLED display screens are their excellent contrast, wider viewing angle and great brightness – plus the fact that they can be produced to very large sizes on any kind of substrate, including flexible ones.
OLED versus AMOLED
OLED display screens are made from thin layers of organic material that emit light when current is passed through them. The pixels can be controlled (with current) using a passive or active matrix.
With a passive matrix, the pixels are activated electrically through the sophisticated control of specific rows and columns that make up part of a grid.
With an active matrix, each pixel has its own little piece of electronics in the form of a number of thin-film transistors that make sure each pixel is controlled and operated properly. The advantage of an AMOLED (active matrix OLED) display screen is that it has a higher refresh rate. It is also very economical with power and works with greater precision.
Not enough resolution for virtual reality
But OLED also comes with its own problems. There are still quite a few that need resolving before applications other than camera and smartphone screens become reliable and affordable.
For instance, there is the problem of pixel ‘burn-in’. Pixels degrade when current is passed through them. And when certain pixels are used more than others (for example if a TV station or product logo is displayed constantly during a film), these will degrade more than the pixels surrounding them. This burn-in then becomes visible as pixels that emit less light. In other words, if you change station after watching a long film, the logo of the previous station may still be slightly visible.
Another reason why certain pixels emit less light is the inherent variation that exists between all of the OLEDs in a screen and all of the thin-film transistors that control the OLEDs – even before they have been operating for a single second. This is inherent to the technology, but can be perfectly compensated for by sending more or less current through the OLEDs so that they all emit the same amount of light. Typically, 6 to 8 transistors per pixel are used in AMOLEDs for control and compensation.
The pixels in AMOLED screens are too large for some applications, such as for augmented reality and virtual reality glasses, where information is projected very close to the eye. The closer the screen is to the eye, the smaller the pixels have to be so that the eye is unable to discern the individual pixels. The resolution is also not high enough for augmented reality applications such as a car window with extra information. And large TV screens with higher resolutions are also always more than welcome.
Two recent results from imec and Holst Centre have taken a step in the right direction:
Fewer transistors = smaller pixels
As we have already said, in AMOLED screens 6 to 8 thin-film transistors are typically used per pixel for control and to compensate for the inherent variation and burn-in. By using fewer transistors, the pixel can be made smaller and hence the resolution becomes higher.
Imec and Holst Centre have developed a compensation scheme that only requires three transistors to control and compensate each pixel. Compensation is achieved by using standard silicon electronics that are located outside the pixel and not by the thin-film electronics inside the pixel itself. Silicon chips such as these are already controlling some screens. They are extremely reliable and fast and do not consume much power. Every so often, readings are taken, based on the 3 thin-film transistors, and a calibration cycle is carried out to determine what the right voltage is per pixel for emitting the required amount of light. This calibration technique is extremely effective, reducing the variation between the OLEDs in the screen from 23% to 0.56%.
Picking the brains of the chip experts
OLED pixels are usually produced by evaporating organic molecules in thin layers on top of each other through a metal mask in order to align the pixels. Imec, which has always specialized in electronic chip research, has a great deal of experience with lithography for producing ultrafine structures for building chips.
This technology – photolithography – is now also used to produce AMOLED pixels that can be made much smaller than with the standard evaporation technique. Naturally the materials, such as the photo-resist, have had to be optimized for this application. Researchers recently produced a (passive) OLED screen with a resolution of 1250 ppi (pixels per inch). By way of comparison, a typical TV has a resolution of 100 ppi. And expectations are that by using photolithography, resolution will be improved to as much as 3000 and even 6000 ppi so that augmented reality applications will be possible.
Want to know more?
- For more technical information about the compensation circuit, you can request the paper entitled “40x current variation reduction enabled by an external VT-compensation scheme for AMOLED displays using a 3T2C-pixel circuit with dual gate TFTs” here. The paper is available from 22 May on.
- For more technical information about the photolithography research, you can request the article headed “High resolution photolithography for direct view active matrix organic light‐emitting diode augmented reality displays”, which appeared as a distinguished paper in JSID journal. The work was published by Pawel Malinowski and his colleague TungHuei Ke (Senior Researcher, responsible for OLED development). The paper is available from 22 May on.
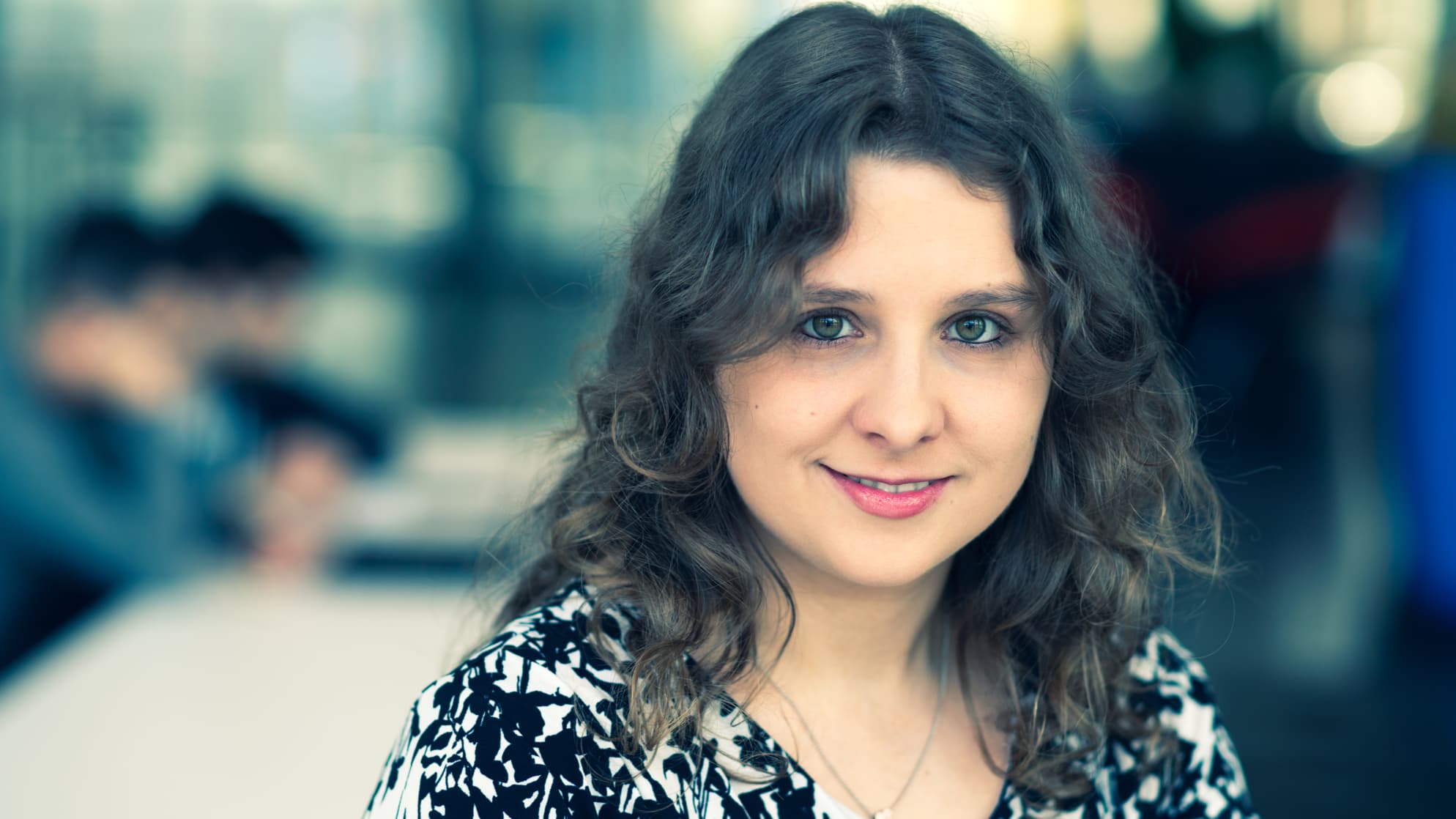
Lynn Verschueren received her MSc in Nanoscience, Nanotechnology and Nanoengineering, focusing on Nanoelectronic Design, from KU Leuven, Belgium, in 2016. Since then, she has been working towards a PhD degree in Electrical Engineering in imec’s Large Area Electronics department. Lynn’s doctorate studies focus on design, driving and calibration for high-resolution displays.
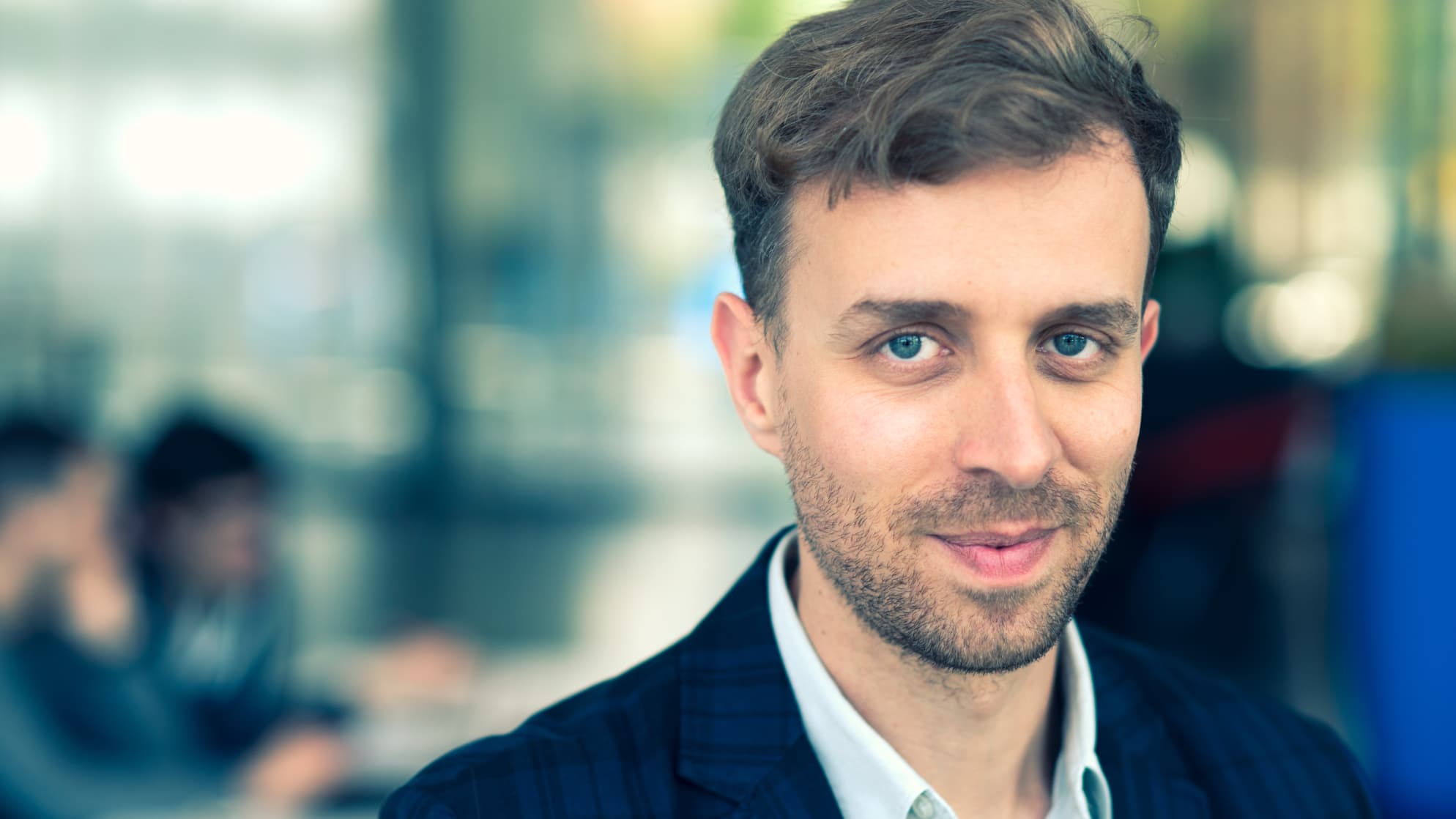
Pawel E. Malinowski gained his MSc in electronics and telecommunications (thesis on the design of radiation-tolerant integrated circuits) from the Lodz University of Technology, Poland, in 2006. In 2011, he was awarded his PhD in electrical engineering from the KU Leuven, Belgium (thesis on III-nitride-based imagers for space applications).
Since 2011, he has been working as a senior researcher and project manager in the Large Area Electronics Department at imec, where he focuses on thin-film image sensors and on high-resolution OLED displays. From 2006 to 2011, he was a PhD Researcher at imec, Leuven, Belgium, working on AlGaN photodetectors and imagers for space applications. Pawel has authored or coauthored more than 30 publications. He was a recipient of the International Display Workshops Best Paper Award in 2014.
Published on:
27 April 2018