Many people are familiar with the biennial World Solar Challenge for student-teams and their solar-powered cars, founded in 1987 to foster the development of solar-powered vehicles and photovoltaics (PV) innovation. Held every two years as a race across Australia, the Solar Challenge Morocco has replaced this year’s edition because of the strict COVID-19 restrictions in Australia. Many people also know that the prototype cars involved in the event are a relevant outlet for automotive (and PV) suppliers to showcase their state-of-the-art technologies while gaining new insights from the production and race. But fewer people know that vehicle-integrated PV (VIPV) is already available as an option in several modern-day cars. And that a few high-tech startups and scale-ups have anxiously awaited to enter the market with PV-powered electric vehicles that can be driven for months by merely relying on the power generated by the integrated PV-panels.
Loic Tous is the team leader of PV cells and modules at imomec, imec’s associated lab at the University of Hasselt, and partner in EnergyVille. His team was closely involved in helping the KU Leuven Agoria student team to fabricate their solar panels in this year’s car, the BluePoint Atlas. And he has a perfect view of the state-of-the-art in commercial VIPV, its realistic future, and the primary research challenges the sector is tackling.
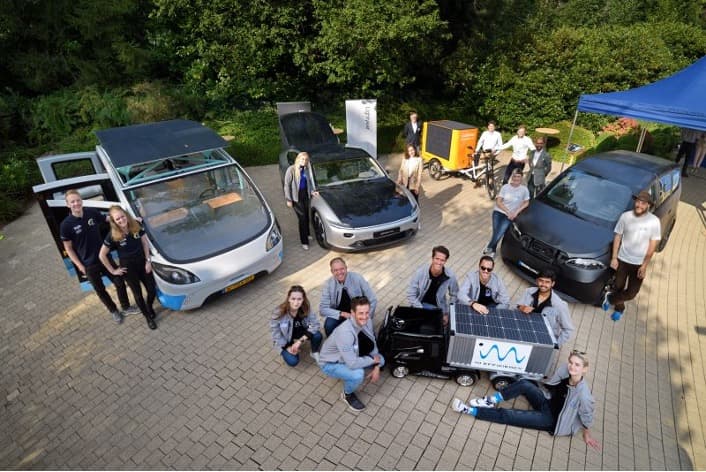
Vehicle-integrated photovoltaics (VIPV): from lab-scale concepts and student prototypes to commercial vehicles. The whole spectrum captured in one image, taken at an event by ASOM, the alliance for solar mobility (© image by Bart Van Overbeke).
The existing market and technologies for VIPV
Loic Tous: “In the nineties, the Volkswagen group introduced a small PV roof as an option in several cars such as the Audi A8, VW Phaeton, Skoda Superb, and others. These PV roofs were very expensive (>2000 euro) and had a maximum power of only 30 Watt peak (Wp) which was mainly intended to avoid ignition problems related to 12V battery drain. In the last decade or so, integrated PV technology has rapidly evolved and is becoming sufficiently cost-effective for larger-scale integration in commercial vehicles.”
Today, the Toyota Prius Prime, Nissan Leaf, Karma Fischer Revero, Hyundai Sonata, and Ioniq 5 are some of the first cars that offer PV-integrated panoramic sunroofs either standard or on their option list. Other automotive brands in the premium segment are following suit. Soon, they will offer similar features, most likely as optional “solar packages,” similar to driver-assistance, business, and other comfort packages. With power outputs in the orders of a few hundred Watt, these PV panoramic sunroofs are mainly intended to support the heating, ventilation, and air conditioning (HVAC) systems. As such, they can annually result in around two to three thousand kilometers of extra range depending on the location and driving profile.
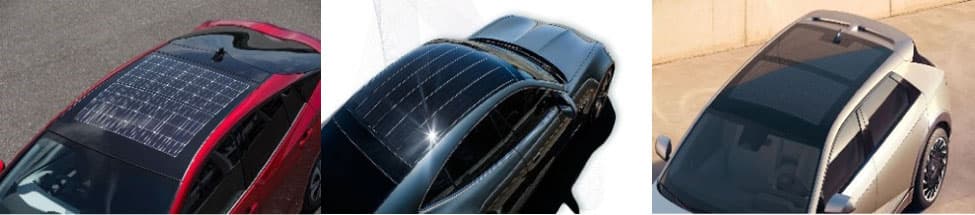
Several commercially available family cars already offer PV-integrated panoramic sunroofs, either standard or on their option list. From left to right: 2019 Prius Prime (Image © Toyota), 2020 Revero (Image © Karma Fischer), 2021 Ioniq 5 (Image © Hyundai).
Loic Tous: “Because of the inherent nature through which automotive manufacturers produce large panoramic sunroofs, integrating them with PV systems is the logical next step. In large panoramic sunroofs, a polymer encapsulant is laminated in between two glass plates to avoid shattering in case of an accident. Laminating additional solar cells in between the glass and the encapsulant adds limited complexity and costs and is, therefore, being seriously considered by the automotive industry.”
But there’s more to it than just gluing solar cells onto one of the existing layers of the sunroof. As a first example, one could look at the already mentioned lamination process. In automotive industries, this lamination is done in autoclave machines that operate at high pressures, which can destroy the PV components. In addition, the autoclave needs a relatively long process time to provide satisfactory results. In the PV industry, lamination is performed with simple membrane laminators, which operate at much lower pressures and are more optimized for higher throughputs and in-line processing. Conventional laminators, however, also have their drawbacks when aiming to apply them in automotive.
Loic Tous: “PV laminators typically use a membrane to apply pressure on one side of a PV panel that is supported by a flat carrier. If you put a curved glass panel inside without any support, the one-sided pressure causes it to break. We, therefore, have a state-of-the-art two-membrane laminator to our disposition at imec in which homogeneous pressure is applied simultaneously on both sides. Within the imec.icon SNRoof project, one of the activities is to compare this approach with the autoclave processes used in automotive. Both approaches can deliver perfectly functional devices, yet the membrane lamination approach is most promising to move towards higher-volume manufacturing.”
Similar examples and research efforts are found in the material choices for the encapsulant (the layer that protects the PV cells from environmental hazards such as humidity, mechanical stress, etc.). The PV industry mainly uses ethylene-vinyl acetate (EVA) or polyolefin (PO) materials as an encapsulation layer. These materials are optimized for minimal penetration of agents such as water or salts but less for impact resistance or acoustic properties. In automotive, the commonly used layer in between the two glass substrates is composed of automotive polyvinyl butyral (PVB), which is well optimized in terms of impact, transparency, and acoustic properties (properties that are becoming crucial in “silent” electric cars). On the downside, it is more hygroscopic, so less suited to protect PV cells against humidity and salts.
Loic Tous: “Overall, one could say that there are two approaches. The industry-conservative approach starts from the existing automotive technologies, materials, and processes to make them compatible with the requirements for PV integration. That’s why for the moment, for PV sunroofs, autoclaves and automotive-PVB materials are being used and optimized for compatibility with PV technology. In the long term, the more scalable solution in terms of cost and throughput could be to start from the technologies, materials, and processes optimized for PV and tune these towards the automotive manufacturing chain. In the more mature – yet equally conservative - market of building-integrated PV (BIPV), we are already in the stage where construction companies have gained enough confidence to move away from architectural PVB and allow for the adoption of EVA or POE. I expect the same to happen in the automotive sector at some point.”
The next step: co-design of car and PV system
The big challenge, however, is to design and manufacture cars where PV integration can practically eliminate the need for regular charging. For the moment, this is the domain of startups and scale-ups such as Lightyear in the Netherlands and Sonomotors in Germany. With their respective cars, Lightyear One and Sion, they aim at generating sufficient energy from the integrated PV panels for the vehicle to be fully self-sufficient on short distances like a daily commute to work.
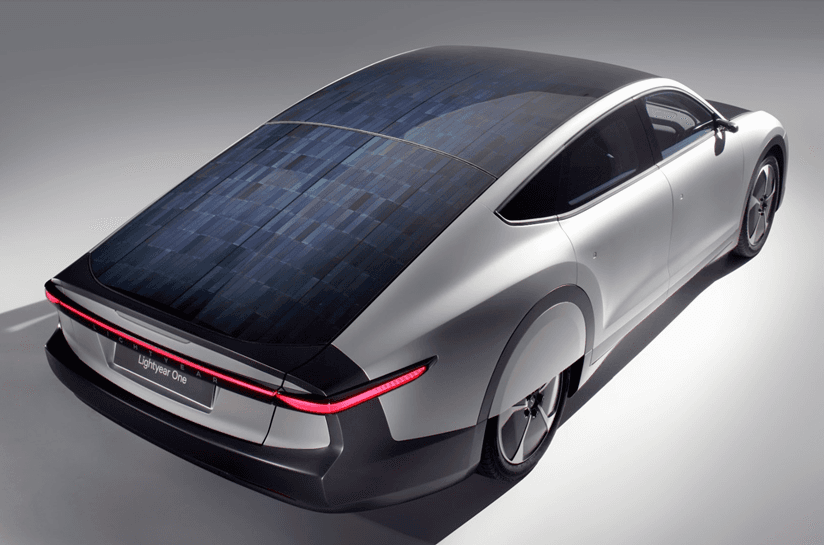
When aiming for PV-powered cars, you have to co-design the vehicle and the PV system and apply PV not only on the roof but also in the body panels. (Image © Lightyear)
Loic Tous: “These companies are aiming at annual range extensions of ten thousand kilometers or more, enabled by the integrated PV modules. Compared to PV-enabled panoramic sunroofs, this would mean power outputs of over a thousand Watts instead of around two hundred Watts. Toyota has built prototype cars with high-efficiency PV cells that are optimized for space applications, but these are far too expensive to integrate into commercial vehicles. To reach these power outputs at an affordable price tag, one must integrate PV modules not only in the roof but also in other body panels. And also, related factors such as weight, aerodynamics, and friction of the tires become increasingly important. In contrast to the more straightforward and compatible process of PV integrated sunroofs, building a fully PV-powered car requires a new approach from the ground up whereby car and PV system have to be co-designed.”
Developing the technologies to support this ambition is quite demanding. For example, in contrast to glass sunroofs, body panels come in a larger variety of materials (metal, plastics, fiber composites). Also, potentially integrated PV systems will need to pass all automotive tests, demonstrate reliability and reach lifetimes of over 10-15 years, and be easy to replace or repair in case a body panel gets damaged.
Imec and partners contribute to the future of VIPV
In this complex reality, imec and its partners are active on various levels to take VIPV and related technologies to the next level. For example, the previously mentioned SNRoof project aims at developing breakthrough technologies for PV-integrated sunroofs. More specifically, it sets itself four high-risk high-gain research goals: (1) developing and scaling innovative interconnection technologies for large-area crystalline silicon and perovskite/silicon tandem solar cells; (2) innovating curved glass coating and lamination technologies that meet automotive requirements; (3) creating shade-tolerant PV cell module layouts using the support of advanced modeling tools and (4) realizing industry-relevant proofs-of-concept for the different generations of panoramic sunroofs. This imec.icon project, funded by imec and Flanders Innovation & Entrepreneurship (Vlaio), is halfway through its two-year timeframe. The consortium of four industrial partners (including a leading supplier of EV-optimized glass panels) and multiple imec research teams are confident they can deliver the foreseen results by the end of 2022.
Another activity in which imec researchers are making significant strides together with the industry is the H2020-funded HighLite project that aims for high-performance, low-cost, and sustainable crystalline-Si PV modules tailored for different applications. Among the partners in the project is Valoe, the Finnish company that supplies PV-integrated body panels to Sonomotors.
Loic Tous: “Much of our own effort in this project focuses on reaching lightweight PV modules for vehicle integration. For example, we are looking into developing next-generation crystalline silicon cells with efficiencies above 23% and innovative shingling technology to optimally use the available surface in the curved body panels. Recently, we reached an important milestone by demonstrating lightweight (< 6kg/m2) prototype PV modules with high-efficiency silicon solar cells that passes several of the critical PV and automotive tests. The goal by the end of 2022 is to demonstrate a complete PV-integrated bonnet. For this, collaboration with industrial partners is crucial. For example, with Applied Materials Italy, which develops the shingling technology and associated equipment.”
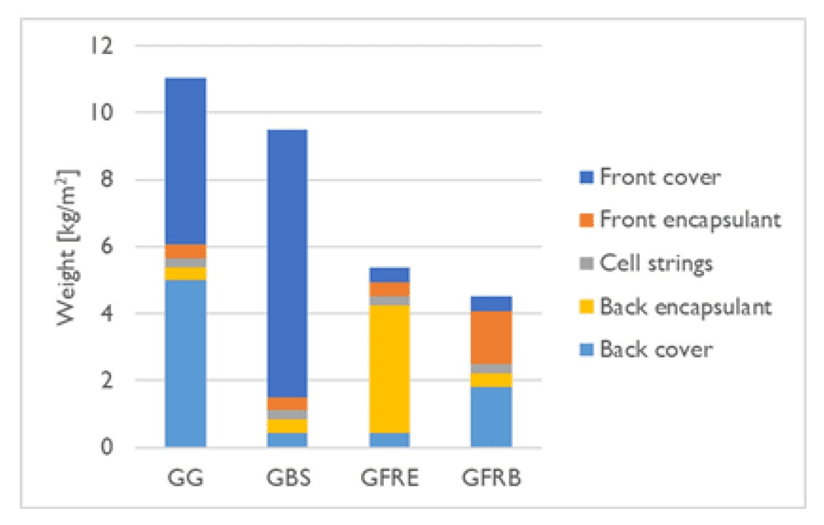
At the 2021 EU PVSEC conference, imec presented two approaches to drastically reduce the weight of VIPV modules by replacing the front or backside glass with glass-fiber reinforced encapsulants (GFRE) or back sheets (GFRB). (Imec solutions on the right show 50% weight reduction or more compared to the typical glass-glass (GG) and glass-back sheet (GBS) approaches).
At the Sept-2021 EU PVSEC, the largest international conference for photovoltaic research, technologies, and applications, imec presented the progress within the HighLite program in full detail. At that same conference, imec also presented a paper about developing and testing lightweight PV modules, whereby two approaches are being compared to replace glass with solutions based on glass-fiber reinforcement. Last but not least, the imec research roadmap also deploys VIPV related activities to compare the use of silicon cells versus thin-film CIGS.
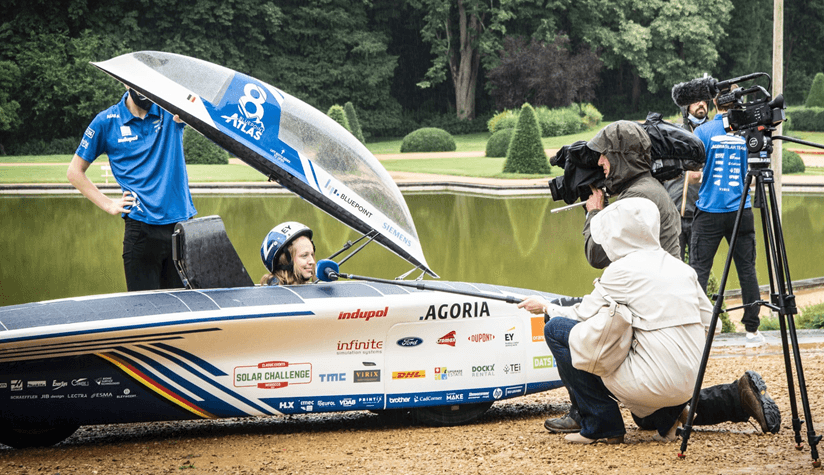
Press announcement of the BluePoint Atlas, the KU Leuven Agoria PV-powered car that competes in the 2021 Solar Challenge Morocco. (image © KU Leuven)
Loic Tous: “We also already have a long-lasting relation with the KU Leuven team that competes in the various editions of the World Solar Challenge. Whereby we have helped them with, for example, our expertise in modeling and characterization. We intensified our collaboration for this year’s Solar Challenge Morocco by giving them technical support and access to our facilities at the EnergyVille Campus in Genk. This advantage allowed them to fabricate the PV modules for the BluePoint Atlas race car using our state-of-the-art two-membrane laminator. This time, the KU Leuven car is not equipped with high-efficiency space cells. These reach efficiencies of over 30% but come at a price of around €100 per cell. The premium silicon cells that the team uses this year reach efficiencies of 23 to 25% and only cost around one euro per cell. The regulations allow the team to cover more surface area with these relatively lower-efficiency cells, so the overall cost-efficiency balance was quickly made. This, however, meant that the silicon cells had to be designed more specifically to fit the contours of the vehicle, and here, the expertise of imec also came into play.”
So, while VIPV technologies are working their way up into the market with a healthy dose of realism, thanks to the R&D contributions by imec and its partners, we will be unconditionally cheering for the KU Leuven Agoria team that competes in Morocco in October 2021.
Want to know more?
- Our publication in OPE Journal
- EU PVSEC papers about the HighLite program and about lightweight PV modules can be requested through this form [add link to contact form]
- Imec.icon SNRoof project page: SNRoof | imec (imec-int.com)
- H2020-funded HighLite project page: HighLite project (highlite-h2020.eu)
- KU Leuven Agoria Solar Team: Agoria Solar Team | BluePoint Atlas
- Imec webpage about PV expertise: Development of high efficient silicon & thin-film solar cell and module technology - imec (imec-int.com)
- Imomec website: IMO - IMOMEC (uhasselt.be)
- EnergyVille website: Research into sustainable energy and intelligent energy systems | EnergyVille
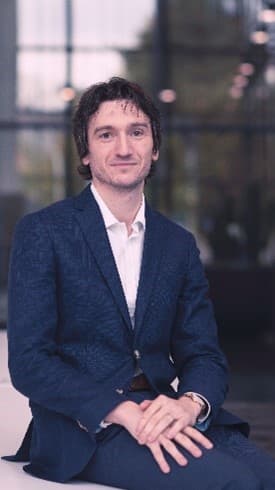
Dr. Loic Tous has been leading the PV cell and module activities at imec since early 2020. He received his Ph.D. in 2014 from the KU Leuven (Belgium). Since 2016, he has been the co-organizer of the Workshop on Metallization & Interconnection for Crystalline Silicon Solar Cells. He is currently the coordinator of the H2020 funded project HighLite (Grant Agreement 857793), which aims to substantially improve the competitiveness of the EU PV manufacturing industry and the research lead of the imec.icon SNRoof project, which deals with integrating into 3D curved roofs of electric vehicles.
More about these topics:
Published on:
7 October 2021