From winning the BEMAS Digital Innovation Award to conquering the petrochemical industry. Jan Coppens and Maarten Weyn, founders of the Antwerp start-up Aloxy, reflect on the success of their technology and the business they have created.
Petrochemicals – and the process industry in general – face an exciting challenge in the transition to the “Industry 4.0” age. This is a new industrial era in which automation, big data and collaboration throughout the whole value chain are encouraging further optimization. At Aloxy we identified two major markets: digital monitoring of the way manual valves operate, and tracking individual parts and assets when a production process is halted temporarily for maintenance.
The limitations of smart systems
The average petrochemical site has anything from between a few hundred to as many as a thousand valves that have to be operated manually. These may involve stopcocks that rotate through more than 360 degrees or levers that move through 90 degrees. Typically, these valves are only used occasionally in processes, so it doesn’t make good cost-related sense to automate them. Yet these valves may also have an enormous impact if they are not kept in good working condition. For instance, you need to be certain that a discharge valve is properly closed before you refill a tank with chemicals after a cleaning operation. But because manual operations, by definition, increase the chance of human error, we wanted to give these companies a little digital assistance.
The biggest challenges here are cost and integration. As we have already said, full integration with existing process automation isn’t the answer because it’s too expensive. So you need to come up with a solution that’s both inexpensive and easy to use. You also want the new technology to add information to the existing systems, but not interfere with the precisely tuned manufacturing processes.
The possibilities of a smart solution
The solution created by Aloxy provides an answer to this delicate technical dilemma. We use our solution to attach an autonomous sensor to, say, the operating hand wheel of a manual stopcock or lever. These sensors contain gyroscopes, accelerometers and magnetometers; technology based on a patent application by imec and the University of Antwerp. This enables us to know how the sensor moves, which in turn also immediately tells us what position the valve is in without having to adjust the installation itself. This information is then sent wirelessly to the control room.
The Aloxy sensor is fitted to the operating hand wheel of manual valves and so is easy to implement.
Our sensors can be retrofitted and are easy to install. The wireless communication is also compatible with current standards (Lora, SigFox, Dash7, etc.). And the software is accessible as a cloud application or can be integrated with the customer’s software.
The system gives the operator real-time information about the status of the manual valves. Using the software that we supply with it, the operator can then use that information in different ways. For example, it is possible to set certain valves to the closed position virtually and to program a warning signal to prevent unwanted operations. Or you can monitor a manual process flow digitally. This can be done by helping an engineer on the workfloor from the control room to carry out a protocol correctly with a number of successive actions.
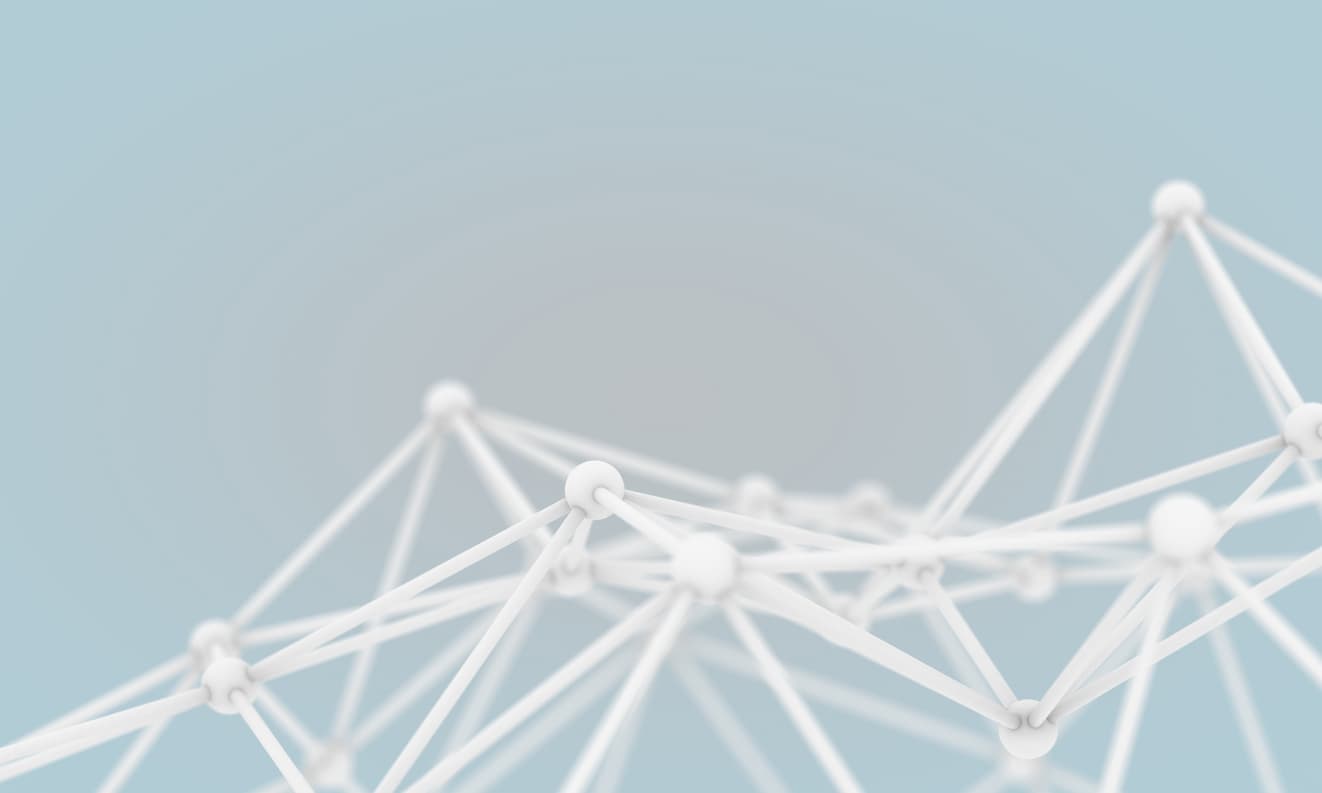
The system gives the operator real-time information about the status of the manual valves.
An extra business case
Another application for our solution is in maintenance and shutdowns. When that happens, certain parts and assets leave the site and it becomes virtually impossible to monitor whether everything is still on schedule. Yet that is precisely the kind of information that is vital for assessing whether production can resume on time.
But because we are able to pinpoint the location of our sensors, we always know whether the parts are in the workshop for repair or are elsewhere in transit.
We are currently working with the energy company Engie to see whether we can develop this use case further.
The Aloxy business
Aloxy was set up in 2017 using our own investment and support from the imec.istart program. The technology was transferred from two proof-of-concept projects and two patent applications from IDLab, an imec research group at the University of Antwerp. It may sound like a cliché, but since then we have been on a real rollercoaster. In November 2017, we were selected to take part in the Plant 4.0 incubator, an initiative from several major industrial players in the process industry. This enabled us to test out proof-of-concept in real operating environments. To monitor our manual valves, we currently have our solutions running with three partners: BASF in the Port of Antwerp and two other companies, in Spain and the Netherlands. These pilot projects are important for validating and further developing our solution. For example, we recently discovered that major vibration levels at industrial sites may be having an effect on our sensors, which is something we hadn’t factored in originally. But we have learnt that our algorithms need to be able to take this into account.
We have had other things to celebrate, too. We received the Digital Innovation Award from the Belgian Maintenance Association (BEMAS) at the Maintenance 2018 in March of this year. This award generated a great deal of visibility for us and boosted our credibility with investors. The next step for Aloxy is to develop our solution further to make it a product that we can manufacture and roll out in volume. We are currently closing an investment round for this. We also aim to apply for the imec.icon program so that we can continue developing our R&D process in conjunction with knowledge- and business partners.
Want to know more?
-
YouTube film clip about Aloxy
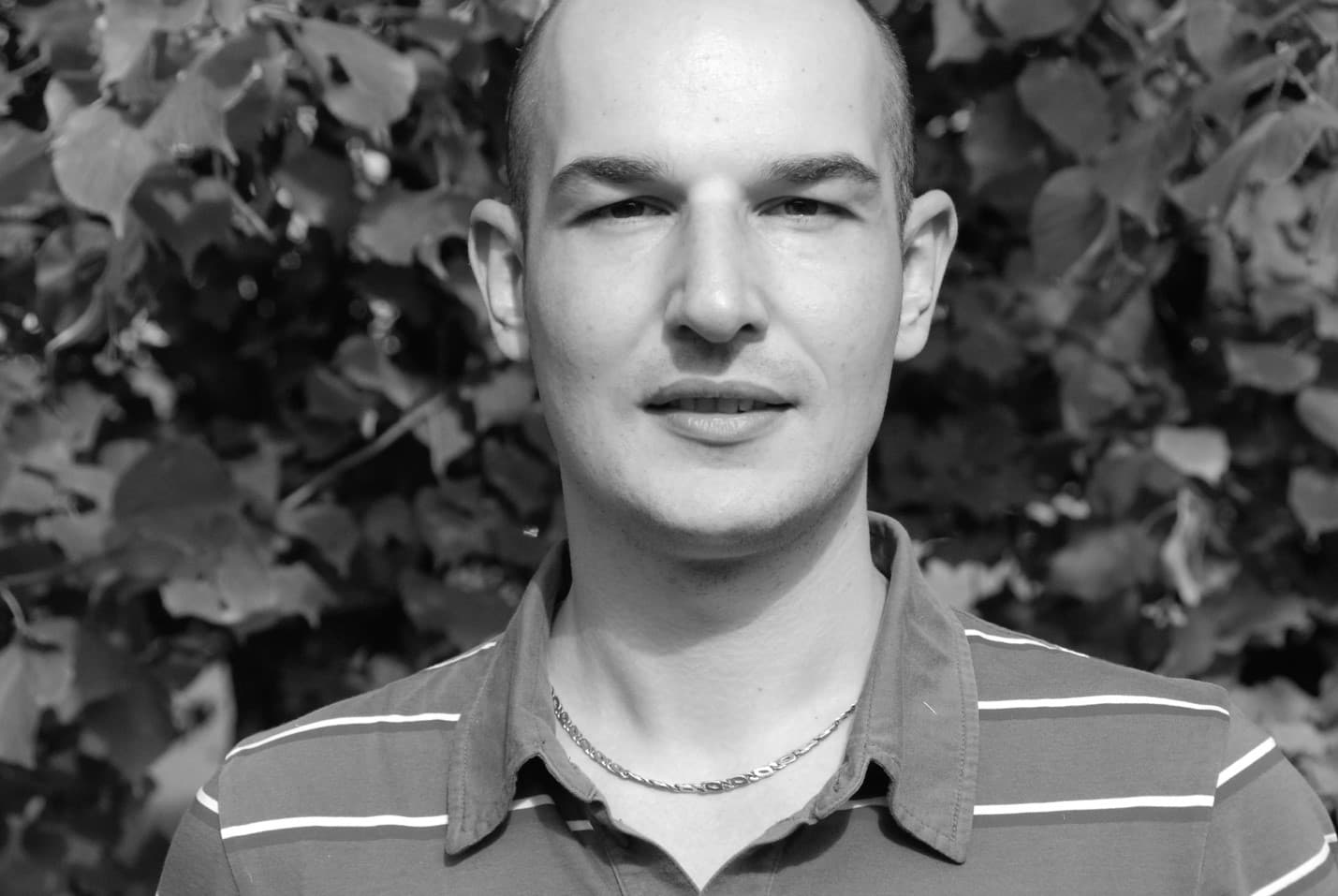
Jan Coppens obtained a PhD in computer science engineering at Ghent University and continued his research in networking technology at Bell Labs. In 2008, Jan joined McKinsey & Company, serving clients mainly in the telecommunication and financial industry. He specialized in IT business strategy, change management and pushed McKinsey’s thinking about Lean application development. In 2011, Jan returned to iMinds (IBBT at the time, now imec) to initiate iMinds’ start-up incubation, acceleration and internationalization programs. Meanwhile, he lectured entrepreneurship at the Master of Global Management at Antwerp Management School. After his role in driving iMinds corporate strategy and structuring the merger with imec, Jan supported the integration of both institutions and founded Aloxy as a spin-off of imec and the University of Antwerp.
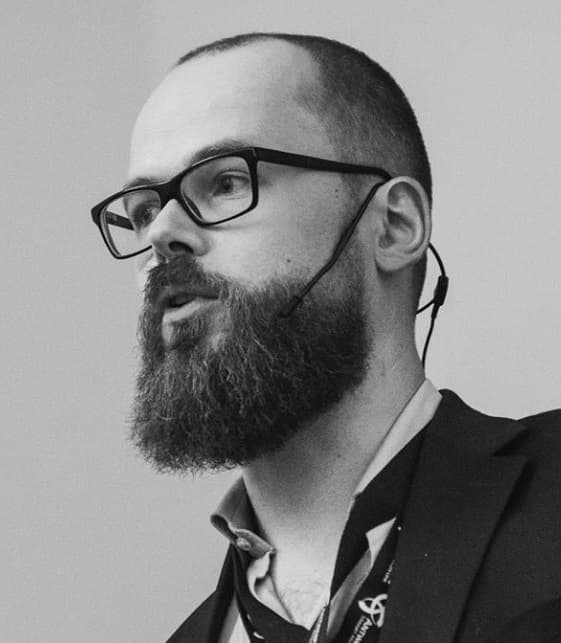
Maarten Weyn gained his doctorate in Computer Science on the topic of Opportunistic Seamless Localization at the University of Antwerp, Belgium. Maarten is a lecturer at the same university and currently teaches in the third year of the bachelor’s degree course for Mobile Communication and Telecommunication and on the master’s course for Communication Systems and Internet of Things: Low Power Embedded Communication in the Department of Applied Sciences: Electronics – ICT, as well as on the postgraduate Internet of Things course on the subject of Context Aware Wireless Embedded Systems. He is also in charge of the Ambient Environments team project for the postgraduate innovative enterprise course taught at Flemish universities.
His work in the imec-IDLab research group focuses on ultra-low power sensor communication and embedded systems, sub 1-GHz communication, sensor processing and location. Most of his projects are run working closely with industrial partners.
Maarten is the co-founder of the spin-offs Aloxy and AtSharp. He is also involved in setting up the spin-offs 1OK and Viloc. He is a director of the dash7 Alliance and promoter of the Open Source Stack OSS-7.
More about these topics:
Published on:
28 June 2018